AC, DC, Servo Adjustable Speed Drives
ISC Companies and affiliate Adams-ISC are distributors of mechanical power transmission parts including adjustable speed drives. For more information about the brands we offer and/or pricing, please contact us by phone 763-559-0033, by email [email protected], or by filling out our online contact form.
AC Adjustable Speed Drives
AC motor speed is based on the number of poles built in and the frequency of the AC voltage applied. In order to change the speed, AC controllers are used to change the frequency of the applied signal by changing the 60 Hz signal to DC and then changing the signal back to AC of varying and controllable frequency and voltage. These controllers are known as inverters. Most use pulse-width modulated (PWM) technology, but current-source inverters (CSI) are also available (at higher HP ratings). Flux-vector drives have a more accurate control strategy than strictly controlling the output volts and frequency for PWM inverters.
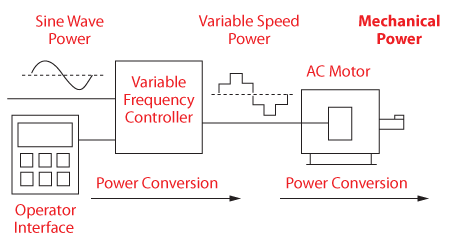
Variable Frequency Drive System
In all adjustable frequency drive (or variable frequency drive) systems, the voltage at the drive motor varies directly with output frequency, up to the rated frequency of the motor. There are two exceptions; during acceleration, some drives boost the input voltage above the constant volts-per-hertz ratio to produce faster acceleration; and, when drives operate above rated motor frequency, they maintain constant motor voltage.
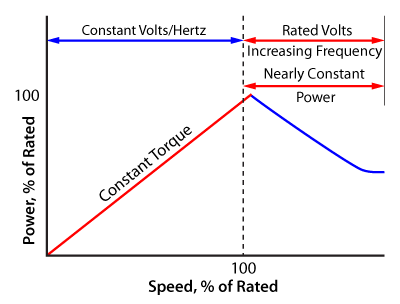
Output Power Versus Speed of Adjustable Frequency Drive
Current Source Inverters (CSI)
CSI drives regulate current rather than voltage. As the frequency of the AC signal applied increases or decreases to control motor speed, the inverter regulates the amount of current that flows through the motor to prevent motor damage. CSI drives can regenerate power back to the input AC line so that braking an overhauling load does not depend on the thermal capabilities of dynamic braking resistors. They are popular in ratings more than 200 HP.
Pulse-Width Modulated (PWM) Drives
In a PWM drive, motor speed is controlled by the frequency of the inverter’s output. However, motor current is controlled by rapidly switching the inverter on and off many times during each cycle. The current waveform is controlled to prevent motor overheating. A typical converter section consists of a full-wave rectifier section, which is unregulated but constant. The inverter section is controlled to pulse the power semiconductors on and off at carrier frequencies from 2 to 20 kHz.
Flux-Vector Control Drives: an advanced control strategy for PWM drives. The AC voltage impressed on the windings of a squirrel cage induction motor consists of two vectors, a torque vector and a magnetic flux vector. Values can be calculated when drive frequency, shaft position, and instantaneous root mean square (rms) voltage are known. An advantage is its ability to deliver a wide and controlled speed range, such as 2,000:1.
DC Adjustable Speed Drives
In this type of drive system, an AC motor drives a DC generator. The generator is an adjustable-voltage power supply for the DC drive motor. DC drives are electrically simple, allow continuous operation in all four quadrants, and cover a wide range of power ratings. Thyristor-type power modules are used for drive ratings from less than 1 HP to over 2,000 HP.
A DC motor with a constant field voltage increases its speed when the voltage across its armature circuit increases, and vice versa. Above the motor’s base speed (maximum rated speed with rated load, armature, and field voltage), speed can be increased by reducing field voltage. Although speed increases and power remains constant, torque weakens. Safeguards must be put in place to prevent motor “run-away” in the event that power is lost in the field circuit.
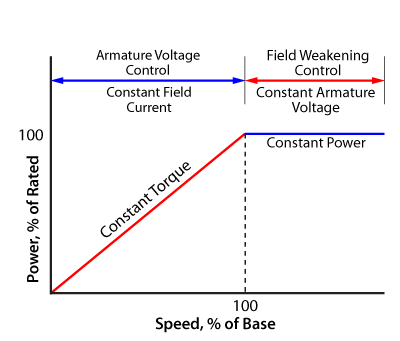
Output Power Versus Speed of a DC Drive with Armature Voltage and Field Current
Most general-purpose drives use digital regulators and some use analog regulators where they need to provide servo-like performance.
A DC drive system consists of both a DC motor and a dedicated speed control assembly. DC drives are available from 1/4 HP to 10 HP for operation from single-phase 115 Vac and 230 Vac power. Motor base speeds vary from 3,450 down to 300 rpm, but not all HP ratings are available at all base speeds. General purpose DC drives are intended to support simple constant torque, 10:1 to 20:1 speed range applications – with and without reversing.
Servo Drives
Servo drives are variations of basic DC and AC drives, the difference is that a servo drive accelerates, decelerates, and reverses a load faster and arrives at a specified position with more precision. DC drives and flux-vector controlled AC drives often provide servo-type performance. Step motors and their controllers also compete with servo drives.
Servo drives are rated in terms of continuous and intermittent torque values over the controlled speed range and maximum acceleration rate rather than horsepower. Top speeds are as high as 9,000 rpm with brushless servo types, 3,000 rpm for moving coil DC drives, and up to 2,000 rpm for thyristor controlled brush-type DC drives.
Top Brands We Offer
Content on this page was created using excerpts from the Power Transmission Handbook (5th Edition), which is written and sold by the Power Transmission Distributor’s Association (PTDA).
You must be logged in to post a comment.