Lubrication
ISC Companies and affiliate Adams-ISC are distributors of mechanical power transmission parts including lubrication/lubricants. For more information about the brands we offer and/or pricing, please contact us by phone 763-559-0033, by email [email protected], or by filling out our online contact form.
The science of interacting surfaces in relative motion is called tribology. It is primarily concerned with the friction, wear, and lubrication of moving parts in instruments, machinery, manufacturing, and technology. Proper tribology has many benefits including decreasing consumption of non-renewable natural resources, increasing energy-efficiency, and prolonging component life. Adding a lubricant to a solid-solid contact will significantly reduce friction, which leads to less wear, heat generation, and energy loss. Proper lubrication reduces operational costs and downtime.
Lubrication is used in almost every mechanical device. The primary function of a lubricant is to provide protection for moving parts by reducing friction and wear. Cooling and debris removal are the other important functions of lubrication.
Fluids and Viscosity
A fluid is a material that is either a liquid or a gas; and fluids include air, water, and oil. Most lubrication is the result of a fluid film that is between two solid surfaces that move relative to each other. The fluid film in the lubricated area can have a thickness ranging from a few nanometers to hundreds of microns thick.
The most important property of a lubricant is viscosity, which is the fluid’s ability to resist motion. High viscosity means that the fluid is thicker and does not flow easily. A higher viscosity fluid will typically make a thicker film between the moving surfaces and support greater loads. However, viscosity is not a constant property. It is dependent upon pressure and temperature. High viscosity does not guarantee a good lubricant. Chemistry of the fluid and conditions and the interface are also factors when determining the proper lubricant.
Temperature and Oil Service Life
Lower oil temperatures lead to a longer oil life. At higher temperatures, oxidative degradation occurs much faster than at lower temperatures.
Lubrication Regime
The thickness of the fluid-film determines the lubrication regime or the type of lubrication. The basic regimes of fluid-film lubrication are:
- Fluid Film Lubrication is the regime in which the load is fully supported by the lubricant within the space between the parts in motion relative to one another object and solid–solid contact is avoided
- Hydrostatic Lubrication: external pressure is applied to the lubricant in the bearing to maintain the fluid lubricant film where it would otherwise be squeezed out.
- Hydrodynamic Lubrication: the motion of the contacting surfaces pump lubricant around the bearing to maintain the lubricating film. This design of bearing may wear when started, stopped, or reversed, as the lubricant film breaks down.
- Elastohydrodynamic Lubrication is mostly for nonconforming surfaces or higher load conditions. Elastic strain at the contact creates a load-bearing area, which provides a gap for the fluid to flow through. Similar to hydrodynamic lubrication, the motion of the contacting bodies generates a flow-induced pressure, which acts as the bearing force over the contact area. In such high pressure regimes, the viscosity of the fluid may rise considerably. At full film elastohydrodynamic lubrication the generated lubricant film completely separates the surfaces. Contact between raised solid features (asperities) can occur, leading to a mixed-lubrication or boundary lubrication regime.
- Boundary (Film) Lubrication: The hydrodynamic effects are negligible. The bodies come into closer contact at their asperities; the heat developed by the local pressures causes a condition which is called stick-slip, and some asperities break off. At the elevated temperature and pressure conditions, chemically reactive constituents of the lubricant react with the contact surface, forming a highly resistant layer or film on the moving solid surfaces (boundary film) which is capable of supporting the load and major wear or breakdown is avoided. Boundary lubrication is also defined as that regime in which the load is carried by the surface asperities rather than by the lubricant.
- Mixed Lubrication regime is between the full film elastohydrodynamic and boundary regimes. The generated lubricant film is not enough to separate the bodies completely, but hydrodynamic effects are considerable.
In addition to fluid-film lubrication, there is also solid-film lubrication in which a thin solid film separates the two surfaces. The fluid viscosity, the load that is carried, and the speed of movement between the surfaces combine to determine the thickness of the fluid film and the lubrication regime.
The Stribeck Curve
The Stribeck curve is a plot of the friction as it relates to viscosity, speed, and load. The vertical axis shows the friction coefficient and the horizontal axis shows a parameter that combines the other variables; fluid viscosity, relative speed of the surfaces, and the load of the interface per unit bearing width. Basically, as you move to the right on the horizontal axis, the effects of increased speed, increased viscosity, or reduced load are seen. The zero point on the horizontal axis corresponds to static friction.
The combination of low speed, low viscosity, and high load will produce boundary lubrication, which is characterized by little fluid in the interface and large surface contact. This results in very high friction.
Machinery will see boundary lubrication at startup and shutdown (low speeds and thin film) before transition to hydrodynamic lubrication at normal operating conditions (high speeds and thick film). The Stribeck curve will show that a machine will experience the most friction and wear during start up and shut down.
Grease
Grease consists of a solid soap such as calcium or lithium, or in some cases, a fine clay that forms a matrix in which a liquid lubricant is dispersed. The matrix does not aid lubrication but is a reservoir that releases lubricant to the contact area. The liquid lubricant can contain boundary and EP (Extreme Pressure) additives as well as solid lubricants such as graphite and molybdenum disulfide.
Grease-Gelling Agents – Soap and Soap Complex
Thickness, while not contributing much toward lubrication, impart unique properties to the grease, affecting its applicability in certain applications or environments. Of these, the lithium and lithium-complex-thickened greases are by far the most common.
- Lithium: Most common, easy to manufacture, easy to store, good pump-ability, resists dust and coal, flow-ability (permits dirt to flow out)
- Calcium: Requires less re-greasing, good water resistance, calcium soap aids lubrication
- Aluminum: Highest resistance to water, chemicals, acids, (edible)
- Barium: High water resistance, somewhat toxic
- Sodium: Fibrous, water-soluble
Non-soap Greases
Another class of thickeners is the non-soap thickeners. These are usually in high-temperature applications., causing the other types of thickeners to soften excessively. This can cause the grease to not stay in place or even cause it to lose its thickness permanently.
- Clays and Silica: Insoluble powders, silica, or platelets of clay. Chemically modified structures and surfaces are made usable as gelling agents for grease. These greases further increase the maximum usable temperature.
- Polyurea: Polyurea greases are called high-performance greases due to their broad range of performance attributes.
Solid Lubricants
A wide variety of solid materials with inherent lubricating capabilities are available for use in solid-film lubricants. The most commonly used are molybdenum disulphide, graphite, and polytetrafluoroethylene (PTFE). Other materials used include tungsten disulphide, baron nitride, lead oxide, antimony oxide, niobium selenide, lead, tin, silver, indium, fluorinated ethylene propylene (FEP), perfluoroalkoxy copolymer (PFA).
No one formulation can satisfy all the requirements on a cost-effective basis. Properties that should be considered are the coefficient of friction, load-carrying capacity, corrosion resistance, and electrical conductivity. Another factor to consider is the environment in which the solid -film lubricant must perform.
Environmental factors include temperature, pressure, humidity, oxygen level, radiation, etc. Each solid-lubricant material has its strengths and weaknesses in each, and corresponding compromises must be made.
Applications of Solid Lubricants
Solid lubricants are used primarily as extreme pressure (EP), or anti-wear type, additives and are applied in one of three ways. First, and most popular, is as an EP additive in grease formulations. The plate-like structure of these solid lubricant particles reduces friction by allowing the surfaces in motion to easily slide over each other. This application is used in applications like pins and bushings. Graphite is particularly useful where moisture is present, in fact the presence of moisture is necessary to ensure the graphite’s full benefit as a friction reducer.
Molybdenum and PTFE are frequently used as anti-wear additives blended with engine oils or other lubricants. However, there is some controversy over the effectiveness of these solid lubricants suspended in oil.
The third and most practical method of applying solid lubricants is the bonding or impregnation of these friction modifiers onto the surface of machine components. The bonded film forms a sacrificial wear film on the surface that is subjected to friction. The bonding or impregnation process can be continually repeated. Critical is the method of bonding the sold films onto the surfaces to be treated.
Binder Selection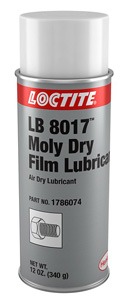
A wide range of resins are available for use as binders or bonding agents in solid-film lubricant formulations. The organic bonding agents are divided into two types:
- Air-dried: Acrylics, alkyds, vinyls, and acetates
- Thermosets: phenolics, epoxy phenolics, silicones, epoxies, polymide-imides, and urethanes
Inorganic bonding agents include silicates, phosphates, and ceramics. Physical properties, environment, solvent resistance, corrosion resistance, and cure temperature are all considerations when selecting the proper product.
Methods of Application
The methods of applying resin-bonded solid-film lubricants are similar to paint-like materials. However they generally need a tightly-controlled film thickness. Major factors that govern the selection of application method include number of parts, size of parts, types of parts, film thickness, tolerance, and spray allowances. Once these parameters have been defined, it can be whether the coating should be applied by conventional spray equipment, electrostatic spray, dipping, roll coating, brush coating, etc. Generally, spray application with multiple coats provides the best lubrication.
Filtration
The number one cause of lubrication failure is contamination. Contamination can arise from outside sources such as water, dust, dirt, etc. or from internal sources such as wear debris. Proper filtration is the first line of defense against contamination, and sometimes, the only line of defense.
Filtration is one of the least understood and poorest implemented tools in preventative maintenance. Most contamination problems are caused by particles that cannot be seen by the human eye. The particles that we most want to eliminate are those that are approximately the same size as the dynamic clearances found in the component being lubricated.
Knowing your equipment and the tolerances (clearances) of its components are critical to good filter application and selection. Filtration can be expensive and excessive filtration can be a waste of time and money. The key is to work with the filter supplier to get the right filter for the right system and to operate it properly.
Degradation and Analysis of Oils in Service
Oil degradation occurs by three methods:
- Contamination (number one cause of oil failure)
- Depletion of additives in the oil
- Direct degradation of the base oil (usually due to heat, oxidation, and similar chemical reactions)
When oil degradation occurs to some point, it is unfit for use, and the machine will not operate properly and will begin to wear prematurely. Most contamination can be handled by filtration, but at some point, base oil oxidation products that enter the oil cannot be removed by practical filtration. Additives become depleted and can no longer do their job. At this point, the only practical action is to drain the oil, thoroughly flush, and clean the system. An oil analysis program can help companies monitor the health of the lubricant and the machine being lubricated.
A well run oil analysis program will do the following:
- Detect abnormal wear in the equipment
- Detect contaminants in the oil, regardless of the source
- Determine the condition of the oil itself
- Aid in determining the proper operating conditions for the equipment
The benefits include:
- Detection of small problems before they become unmanageable
- Reduction of overall operating costs
- Reduction of unscheduled downtime by catching failures before they occur
- Optimization of drain intervals
- Determination of proper filtration techniques and equipment for specific service conditions
Storage of Lubricants
The proper storage of lubricants is also an often-neglected part of a good maintenance program. Storage is an issue of cleanliness, safety, and environment. The three C’s of storage are CONTAMINATION, CONFUSION (what the product is and what it is used for), and CONTAINMENT (to prevent environmental pollution).
A single location for storage is preferred to help with inventory control. Most lubricants are in cans and drums, which should be in a covered area on racks, shelves, or pallets. Drums should be stored on their sides, especially if stored outside or in unheated areas where water can condense in the drum and cause contamination. Proper labeling is critical to eliminate the possibility of a mix-up. One significant source of contamination is transfer containers. For example, a dirty pail being used to transfer a small amount of lubricant from a properly stored, clean oil drum to the machine. Proper protective gear should be worn by the person dispensing the lubricant. And storage areas should be properly blockaded to contain spills.
Aftermarket Additives
It is a common thought that adding some special material or magic ingredient to the lubricant of an industrial machine will cure incorrect operation, misalignment, mismanagement, poor maintenance, etc. Aftermarket additives is probably the most contentious subject in the lubricant market.
Generally, there are no specifications covering these additives. Machine manufacturers or lubricant manufacturers do not approve of the use of aftermarket lubricant products, primarily because there is no control of their quality or use. Many OEMs and lubricant formulators will not honor warranties if aftermarket additives are used. Modern lubricants have as many as 10+ additives that are carefully blended with an emphasis on compatibility and operation efficacy. These additives make up as much as 20% of the lubricant. The addition of an aftermarket additive could cause incompatibility, causing catastrophic failure of the formulation.
When purchasing lubricants for expensive machinery, one should only purchase those that meet OEM specification for the lubricant. Adding aftermarket additives defies that specification. The appropriate oil analysis program will help to get the most out of the lubricant and the machine. Sometimes, lubricant manufacturers will sell specific additive packages, but this is only when oil analysis indicates that this is the proper corrective action.
Selection Criteria
The most important consideration is to use a lubricant that meets or exceeds the lubricant specified by the equipment manufacturer.
The first step is to determine the needs of your company like the volume of lubricant used, the type of equipment to be lubricated and how critical the equipment is to the operation, and the geographical location of the operation.
One option is to provide your lubricant supplier with a complete list of your equipment that requires lubrication. Then allow the supplier to decide which lubricant to provide. Another option is to provide a list of current lubricants being purchased and allow prospective suppliers to provide equivalents. However, there is a risk that the supplier may not have access to exact equivalents. A third option is to provide a list of the lubricant specifications required for each piece of equipment. The lubricant supplier is then required to supply lubricants that meet the specifications and to certify that they do so.
View Line Card | View All Line Cards
Top Brands We Offer
Content on this page was created using excerpts from the Power Transmission Handbook (5th Edition), which is written and sold by the Power Transmission Distributor’s Association (PTDA).
You must be logged in to post a comment.