Industrial Sensors
ISC Automation (a division of ISC Companies) is a supplier of industrial automation components and is a UL508A/698A listed panel shop that designs and builds custom control panels for industrial applications. For more information, please contact us by phone 763-559-0033, by email [email protected], or by filling out our online contact form.
Sensors are devices that respond to a physical stimulus and react by producing a signal that is used for measurement or control. Sensors that are frequently used in power transmission are speed, position, physical presence, liquid level, and pressure.
Tachometer Generators
Tachometer generators measure the rate of a rotating shaft using an internally generated electrical signal. They output a voltage proportional to the shaft speed, which is read by a tachometer and displayed on a readout or fed to an external device. The three basic categories are direct current (DC), alternating current (AC), and permanent magnet. They are frequently used to measure the speeds of electric motors, engines, and the equipment they power: conveyor belts, machine tools, mixers, and fans.
Rotary Encoders
Rotary encoders, or shaft encoders, convert angular position or speed of a shaft to an analog or digital signal. They produce a pulse every time a shaft rotates through a specified angle.
Incremental: Provide cyclical outputs when the encoder is rotated. Types include mechanical, optical, or magnetic. Incremental encoders are inexpensive, resistant to vibration, and provide position and speed data down to zero rpm. They use a rotating disk with etched gratings and a stationary mask with etched slots. A light passes through the mask and disk slots to produce pulses that are detected by phototransistors. Position information will be lost with power interruption.
Absolute: Produce a unique digital code for each distinct angle of the shaft. The two basic types are optical and mechanical. They provide multiple tracks and each have a light source. The alignment is unique for each increment, so position data is not lost due to power interruption. Advantages over incremental encoders: better position data, can be used in higher speed applications, and don’t need a referenced starting point. But, they are more expensive.
Resolvers
A type of rotary electrical transformer that can be used in a variety of position and velocity feedback applications. The most common type is the brushless transmitter. It’s like an electrical motor because it has a stator and rotor. However, the rotor contains a primary winding that has a specified AC signal, called a reference signal, applied to it. The stator contains two secondary windings that are arranged 90 degrees from each other. As the rotor rotates, output voltages create signals to provide shaft position data. Resolvers are rugged and a good option for harsh environments.
Proximity Sensors
Proximity sensors detect the presence of objects without any physical contact. They can operate at higher speeds than limit switches, can sense objects coming from any direction, and are typically not dependent on weight or size of an object to produce a signal output. Some types include capacitive, inductive, eddy-current, hall effect, Weigand effect, photoelectric, ultrasonic, radar, field effect, radio absorption, and magnetic.
Limit Switches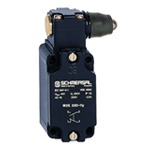
A type of sensor that detects presence and absence of objects. Mechanical limit switches are mechanically activated, meaning they have some type of arm, lever, knob, or plunger, which is physically activated when it makes contact with an object. Eventually the object pushes the actuator to its limit, which is where the contacts change state.
Liquid Level Sensors
Commonly used in continuous and batch control process systems. Some indicate when liquid levels have reached a certain point such as magnetic and mechanical float switches, which is used to automatically control pump motors that regulate levels. Another type is the bubbler sensor, which contains no moving parts, making them suitable for measuring the level of sewage, drainage water, sludge, or water with suspended solids.
Pressure Sensors
Pressure sensors measure pressure, typically of gases or liquids. Pressure is an expression of the force required to stop a fluid from expanding. A pressure sensor usually acts as a transducer; it generates a signal as a function of the pressure imposed.
The three most common pressure sensor technologies are strain gauge, piezoresistive, and capacitive type sensors. These types of electronic pressure sensors generally use a force collector (such a diaphragm, piston, or bellows) to measure strain due to applied force over an area.
Photoelectric Sensors
A photoelectric sensor, or photo eye, is a type of proximity sensor used to detect the presence of a moving target by using a light transmitter (often infrared) and a photoelectric receiver. There are two techniques. In one technique, the target interrupts light going from a source to a sensor. And in the other, the object reflects or absorbs light via a reflective path. There are three commonly used types: opposed (thru beam), diffused (proximity), and retroreflective.
Content on this page was created using excerpts from the Power Transmission Handbook (5th Edition), which is written and sold by the Power Transmission Distributor’s Association (PTDA).
You must be logged in to post a comment.